Q&A with ABB Motion Services’ Oswald Deuchar
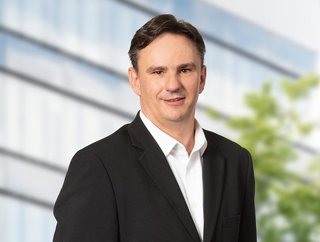
When equipment starts to reach the end of its life, what do you do? Oswald Deuchar, Global Head of Modernization Services at ABB Motion Services, waves the flag for modernising equipment with new components rather than replacing an entire asset.
This is particularly applicable in the energy industry, he advocates. Studies show that the modernisation of existing equipment extends its lifetime but also optimises the performance, all while reducing waste.
ABB research shows that all too often, energy and power businesses will wait until their motor-driven equipment comes to the end of its life before fully replacing the system. This, as Deuchar will go on to explain, isn’t always necessary and can result in costly unplanned downtime which can cost typical energy businesses up to US$180k per hour, as well as a lot of unnecessary waste and scrap material.
Deuchar has worked for ABB since 2006 and has worked in a variety of its business areas, including mining and hoisting.
In this Q&A with Energy Digital, Deuchar shares how operators can modernise equipment to bring it back into its active life cycle, and how this can benefit both the company and its impact on the environment.
Why is it better to act before equipment reaches the end of its life?
It’s essential for energy businesses to have a strategy in place to manage their ageing assets before they reach the end of their life cycle, which potentially might cause costly downtime.
According to a recent ABB survey, unplanned downtime can cost typical energy companies US$180,000 per hour. To avoid this, operators can act proactively and modernise existing assets rather than wait until the equipment becomes obsolete.
What does modernisation involve?
Modernisation is a proactive, efficient and cost-effective way of improving plant reliability and
performance. Some of the options, for example, upgrade and retrofit, involve upgrading only the critical internal components that need replacing, avoiding unnecessary scrap and downtime while also providing the benefits of newer technology.
Consider a variable speed drive (VSD) that controls a motor’s speed and torque to match the exact demands of the task. When modernising a VSD you have an option to retain the cabinet and cabling and just replace the internal components that need changing.
This way, modernisation gives you all the benefits of a new VSD, including lower harmonics, improved serviceability, greater reliability and improved performance. It extends the equipment’s life by 10 to 15 years and avoids unnecessary downtime. This can often be carried out within a normal scheduled maintenance period, minimising disruption.
How does modernisation avoid emissions?
By replacing only necessary components, waste and emissions associated with scrapping, transporting and packaging functional parts of the equipment can be reduced. It’s like only changing the filament in a lightbulb rather than buying a whole new one.
For example, modernising a VSD can avoid up to 55% carbon emissions compared with a complete replacement. Take Swedish utility firm Jämtkraft, for example. It avoided 10 tonnes of CO2 emissions by modernising nine VSDs to bring them back into the active phase of their life cycle. These emissions savings are the equivalent of taking a petrol car off the road for five years.
Because the same cabinets were used for the drives, no major changes were needed to the previous infrastructure. This reduced the overall expenditure for the project. So, by adopting modernisation, businesses not only benefit operationally and financially, but also contribute to wider sustainability and circularity efforts.
In what way is modernisation a more circular approach to replacement?
Purchasing something, using it, then scrapping it at the end of its life is a linear economy – it does not make the best use of a product’s resources. Instead, modernisation is a more circular approach as it aims to maximise resource use and reduce waste. It involves the reuse and refurbishment of components, rather than scrapping them and contributing to landfill. This helps create closed-loop systems where resources are used fully throughout their life cycles.
This concept underlines the importance of designing products with circularity as a priority. The goal should be to make equipment that is durable and repairable and produced with materials that can be easily recycled when the time comes.
This also means that energy businesses have a responsibility to invest in circular products and services. Modernisation is a prime example – by integrating this approach into their maintenance strategy, businesses can avoid downtime, emissions and waste.
*******************
Make sure you check out the latest edition of Energy Digital Magazine and also sign up to our global conference series - Sustainability LIVE 2024.
*******************
Energy Digital is a BizClik brand.